Hopefully you have now purchased and received your new sequential gear system manufactured in house by Pfitzner Performance Gearbox. We would like to help you understand the various methods in which these systems can be used, installed and integrated into your car. We help explain some key information that will allow you to ask the correct questions and help you understand the best methods for installation into you're project. Lastly, we always say, if in doubt! Ask. We are a friendly team here at PPG and we are here to help.
What do I need to know?
Firstly you need to know what your new system is capable off! 99% of the time you will need the help of a expert in ECU calibration. You will also need to install the components into the gearbox case and for that you many need to seek one of our many experience installers.
Engineers, engine & gearbox mappers; calibrators vary in degrees of knowledge on the correct and best practice of programming sequential gear systems. We would like to provide a resource of information to enable a successful installation and calibration to give you years of good service and performance.
-
How are you going to operate? Lever shift or paddleshift?
-
What type of ECU do I have?
-
Is my ECU mappable and able to provide any gear functions?
-
Do you have access to the ECU?
-
Do I have cable or drive by wire (DBW) throttle?
-
Does my ECU have basic or advanced gear features?
-
Is my ECU OEM with aftermarket software available?
-
Do I have access to a local calibrator for my ECU?
Types of Installation
A awesome video from Motive DVD "What the Fast" they take a look at manual & sequential transmissions and explain the different parts of them.
A helical and straight cut the same size, a helical is generally stronger due to the amount of teeth engaged at one time, it’s just that a straight cut can often be made to fit into a small space so in a small gearbox you can make a stronger gear than factory. It also has less axial load, so less stress on shafts and casing, so a small gearbox doesn't need as much strengthening with straight cut. Overall, there is no general rule to which is stronger, it comes down to application and design, obviously the team at PPG are biased :-)
Gear Lever Operation
This is the standard option for sequential gearboxes and allows the driver to operate with a pull for upshift and push for downshift. The lever allows very good installation and very smooth gear changes can be calibrated. The normal operation of the system will be via a solid rod; linkage or Series 4 push pull cable. Each of these options comes with its benefits and enables the design to be optimised within the boundaries of the OEM installation.
The gear lever option has several variations available and calibrators decided based on the ECU systems ability as to what is best suited. As A company we always encourage end users to use a closed loop installation taking full advantage of any DBW (drive by wire) capability the ECU system may have.
Gear Lever – No ECU Control
This is the most basic installation and can yield great performance if the driver has the ability to modulate the throttle on up and down shifts simulating an engine cut. The method has its inherent risks and can allow power on shifts that can destroy the dog rings and put excessive strain on the drivetrain. Ideal for Hot Rod and historic carburetor type application where electronics are not wanted.
Gear Lever – Load Cell - Strain Gauge
In its very basic form the load cell method enables the calibrator visibility of when the driver is applying pressure or force to the gear lever. This information allows the calibrator to use this information to decide when and how long to cut the ignition or fuel in the ECU system to allow the torque on the transmission to reduce and allow the change to occur.
This system is widely used in lower tier racing as it offers a degree of simplicity but stops teams from automation of the gearshift phase. At PPG we don’t recommend this type of installation, basic cut time can cause power on engagement if the driver misses a shift which will result in damage very quickly.
However not all Load Cell based systems require an aftermarket ECU system to provide the cut phase. On many muscle cars in the USA we recommend to clients with OEM - factory ECU’s the “Lingenfelter cut box”.
This box will accept the load cell voltage and provide a cut based on force and time, therefore it is possible to determine the force at which to cut and the amount of time the cut should be maintained. We recommend customers cut based on barrel position and the initial movements they make to determine the cut start.
The system is very basic in its functionality but does provide some great installation and results with again the caveat of no protection should the driver miss shift during the shift phase.
Pseudo Closed Loop – Load Cell & Rotary Position S
This is a system that allows the usage of both the load cell and the rotary position to create a closed loop system using only basic ignition cut signals, such as with the common AEM ECU system. Currently they only support the most basic gear cut strategies and as above this can cause many problems should the driver have a failed shift using a time based cut strategy.
The EASY SHIFT from GEARTRONICS takes both input signals and uses the force to enable the cut and the rotary position voltage to signal the next gear state allowing the power to be handed back to the engine when the correct voltage is seen. They are a pretty smart box of electronics and for less than $600 you can have a system that offers a further degree of performance over basic timed cut; however they offer zero functionality to alter the 100% cut signal and zero ignition retard that a more advanced ECU can provide.
Gear Lever – Closed Loop Gearshift Operation with Integrated Rotary Position Sensor
This system is the optimal configuration for any sequential gearbox installed using lever operation. There are many variants, but to cover the main topic we will consider a gear lever with a load cell and sequential gearbox with a position sensor to read the rotary position of the sequential selector barrel.
Once you have a basic understanding of gear shift strategies you will understand why PPG’s exclusive technologies in the sequential gearbox market set them apart from any of their nearest competitor offerings.
The pioneering usage of the Gill Blade 360º sensor for rotary barrel position back in 2010 marked a turning point in data retrieval in transmission technology and turned a page to enable ECU calibrators to have previously undreamed of data acquisition. This system allows closed loop Motorsports ECU systems to see shift times down to as low as 38ms next gear stable.
This beautiful JM-Imports R34 running a full closed loop system via a Syvecs ECU control system, calibrated by the formidable Romain Levesque of Uk based Race Cal Ltd. You can hear the throttle blips on the downshifts and the seamless upshifts, enabled via a DBW (Drive By Wire) throttle body. Also note how stable the car is during its shift phase. Key to a great package.
In-car in the R34 you can see the clutch is never operated during normal driving, even at low speeds! The car rev matches effortlessly on the downshifts. The lever has an in built motorsports load cell which works in closed loop with the Gill Blade 360º rotary sensor. You can see Romain never needs to use the clutch on either up or downshifts, regardless the road speed.
SHIFT PHASE

RECOVER PHASE

REARM PHASE

IDLE PHASE

Paddle Shift – Air Shifted
We offer several options for paddle shift systems and installations. As a company we limit the amount of components we manufacture for paddle shift systems, instead working with Specialist companies whom offer complete systems. This allows us to focus on the design and installation of the pneumatic cylinder to the gearbox.
This option is in most cases a bolt on addition to the existing system and allows seamless integration to the OEM platform.
Our selected partner SHIFTEC based in the UK has over 15 years experience in paddle shift engineering; designing and Manufacturing components to meet the exacting needs of the dynamic world of professional motorsport. All current paddle shift options come with a custom SHIFTEC pneumatic cylinder supplied and installed so customers can select any third party system they desire.

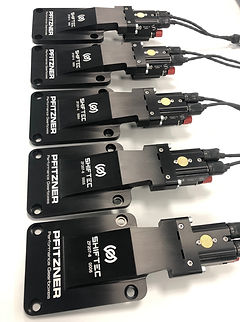

Gear Control Terminology
Closed Loop Gear Shift – Gear Lever
Closed Loop gearshift is the best and safest scenario for a sequential gear system. This state uses the key sensors we supply to enable as much visibility to the ECU as possible to avoid any power on shifting or forced downshifts. The load cell provides the ECU with the force input and the calibrator decides the point at which to start the cut phase, this is usually the point at which the barrel system starts to rotate. This requires some data logging to be reviewed so you can see the max force and force at which rotation starts.
Once the data is reviewed, the force of rotation; for example 14nm is reached the engine will enable the ignition cut to start and this will allow the gears to be disengaged and moved to the next gear position. Once the movement starts to happen on the selector barrel the rotary sensor takes over and sends a voltage output to the ECU. The calibrator in setup has already setup his system and logged the voltage in each gear to allow the ECU to know exactly what gear and state it is in.
Flat Shift
Flat shift is a term used to describe a gear shift where the throttle remains at 100% and the gear change is completed. This is achieved using ECU calibration that allows very accurate ignition and fuel cuts to allow the gearbox to reduce the torque and load on the gearbox. Once the ignition cuts take effect the gear can be moved into the next higher gear. Flat shift can be very complex in modern ECU systems with lots of data and sensors contributing to this import phase of a sequential gearbox. Correct flat shift calibration can make sure the chassis stays balanced and seamless and in return provide the driver with a very neutral and balanced chassis during the gear change phase.
Next Gear Stable
Next gear stable can be defined by dog ring position being in such position of engagement the gearbox can accept torque back and the gear shift will be completed. Typically next gear stable can be set with per gear offsets to allow the gearbox to return torque once, for example 80% engagement. This can allow gear changes to be completed and returned to full power sooner; which we all know results in faster lap times.
Throttle Blip Downshift
Throttle blips on downshift allow gear speeds to be equalized which allow accurate and fast downshift changes under deceleration. Failure to have correct matching gear speeds lead to wheel lock up and chassis instability. Correctly calibrated throttle blips decrease lap times.
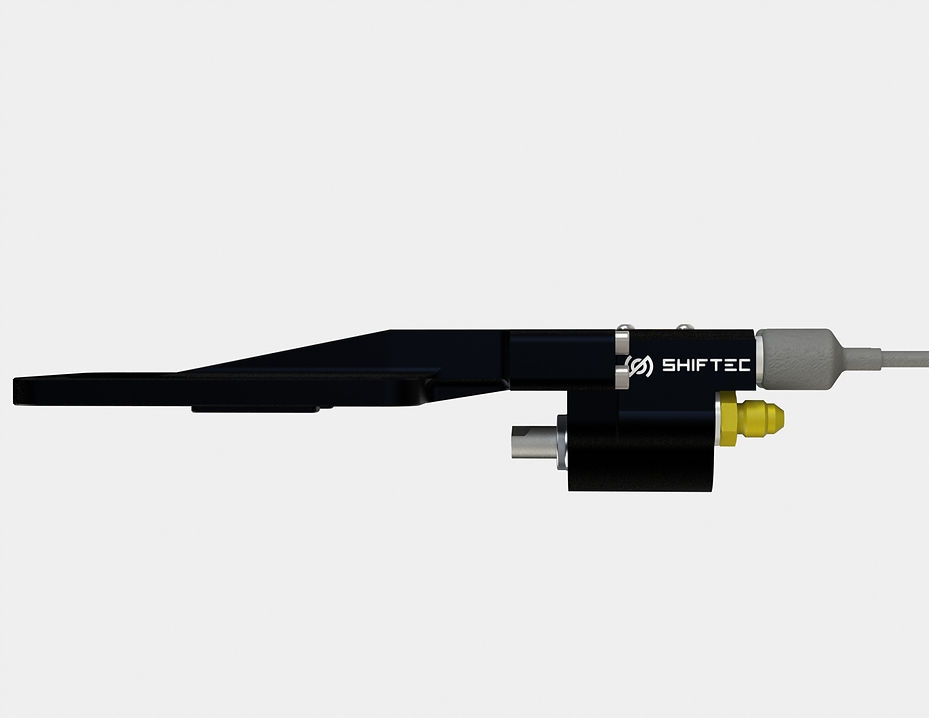
